AeroShield Materials Highlights Key Process Inputs with Process Failure Mode and Effects Analysis
AeroShield Materials, based in Boston, MA, manufactures super-insulating, transparent inserts for windows, based on a breakthrough in silica aerogel research. In an engagement that started with mapping the process in-person, we worked with a cross-functional team at AeroShield to analyze process risks, ending with a Failure Mode and Effects Analysis (FMEA) that prioritizes risk reduction activities.
Challenge:
The technical team at AeroShield is focused on producing aerogel inserts reliably via its unique, multi-step process to further its commercial engagements. Since the process is complex, the leadership wants to perform a thorough process risk analysis in order to highlight areas that are most impactful for continuing to improve quality and yield.
Countermeasures:
Thanks to a grant provided by the Massachusetts AAPI Commission, we provided AeroShield Materials with 4 hours of consulting service. We held focused sessions to work on the three parts of a process risk analysis:
1. Process Mapping
AeroShield provided an in-person walk-through of its manufacturing facility and an overview of its process. Together, we created a process map to capture the inputs and outputs of each process step, starting with raw materials and ending with the final product.
2. Cause and Effects Matrix
A team of subject matter experts gathered to list and rank different customer requirements. We then ranked correlation between the requirements and each of the process inputs captured previously. The team divided up to tackle a long list of process inputs and offered each other their perspectives. We selected several high-scoring process inputs to focus on in the next step
3. Failure Mode and Effects Analysis
In this step, the team dove deeply into the process inputs to identify potential failure modes, failure effects, and potential causes. We then prioritized the causes according to severity, occurrence, and detectability. High priority causes flagged by this process were then assigned mitigation / follow-up actions.
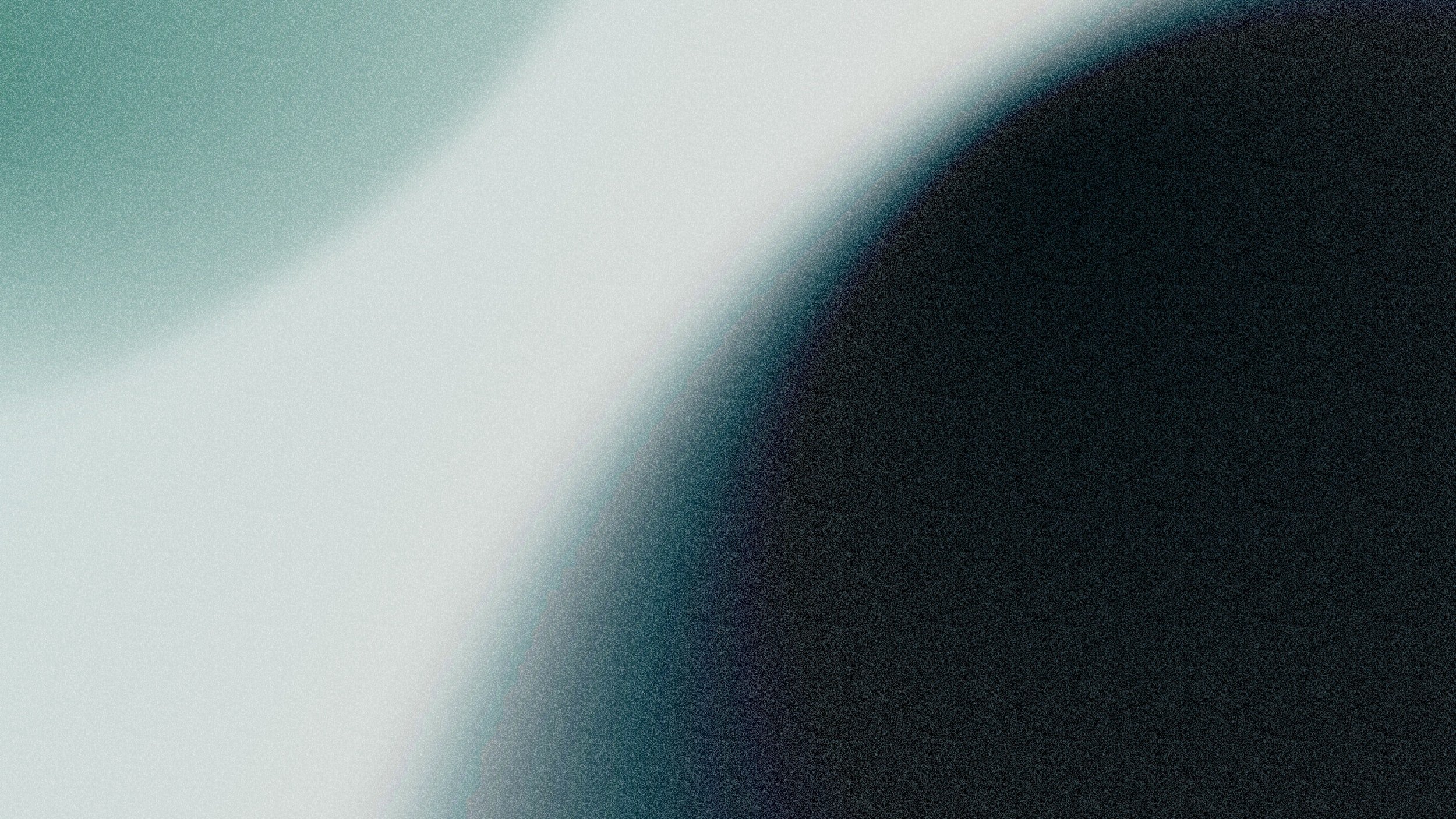
Value created:
We worked with the team at AeroShield to create a highly detailed first version of process risk analysis documents to help prioritize its future development and process improvement efforts. Five AeroShield team members gained hands-on experience on performing a risk analysis and have the know-how to iterate on it independently in the future.
“We have done an FMEA before, but it was time-consuming and not always useful. This one with a focus on process was very helpful.”
-Kyle Wilke, CTO at AeroShield.
Lessons learned:
With the limited time and a plethora of inputs and observations to discuss, we focused on the overall flow, the analytical thinking, and group discussions to build team consensus, rather than rushing to complete the entire analysis.
Teamwork in the Cause and Effects Matrix and the Failure Mode and Effects Analysis is especially important. Since operational, technical, and customer perspectives all factor strongly into rating and comparing different inputs and how they can fail, it is essential to have experts from each area represented. The process of discussing what we enter into each spreadsheet cell, although tedious, is key to building awareness and consensus. The collaborative nature of this process is one way by which the team can “see together, learn together”.